Project Management
At Clancy & Theys, we serve as general contractor and construction manager for every project we take on. That means providing comprehensive construction services tailored to the complexity of the project. In our industry, the trend is that big construction companies no longer self-perform any work. We still do.
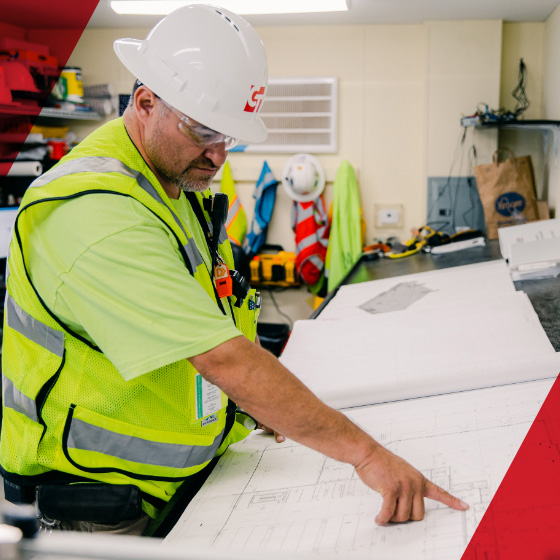
Project Tracking and Reporting
During the construction process, we use comprehensive cost management and project administration software to manage cost reporting, payment applications, contingency tracking logs, potential change order logs, actual change order logs, Interaction Reference Numbers (IRNs), RFIs, architectural field directives, owner requests, minutes, contracts, correspondences, and all other project information. We’re able to combine all project and cost information to give our team and our clients a single source of real-time information related to the project.
We apply the latest technology and project management tools to get the job done, but we are builders first and foremost.
Our roots and our boots are grounded not in paper or on a tablet but on jobsites. We expertly plan and execute getting buildings out of the dirt with concrete and steel and finish them with the highest-quality materials and systems. Project management at Clancy & Theys includes three key processes: project tracking and reporting, Requests for Information (RFIs) and shop drawings, and quality control.
We develop monthly reports to the owner with all relevant documents and images to show project status. This report will include:
- Shop Drawings and Submittals
- Requests for Information
- Daily Reports
- Completed Work
- Schedule Progress and a 30- to 60-Day Look-Ahead
- Cost Update and Change Order Summary and Proposed Change Orders
- Construction Issues and Solutions
- Summary of Inspections and Quality Control Measures
- Percent Complete to Substantiate Payment Applications
- Safety/Accident Report
- Reports on Minority and Women, Disadvantaged, Small and Veteran owned businesses (MWSBE)