Preconstruction Sequencing & Logistics Planning
A detailed preconstruction schedule and effective logistics planning are among the first steps in ensuring a successful construction project. Creating a realistic and detailed schedule for all design, approval, estimating, and purchasing activities help ensure that construction activities begin as planned. Having an effective logistics plan in place before construction begins ensures a smooth transition from preconstruction to construction.
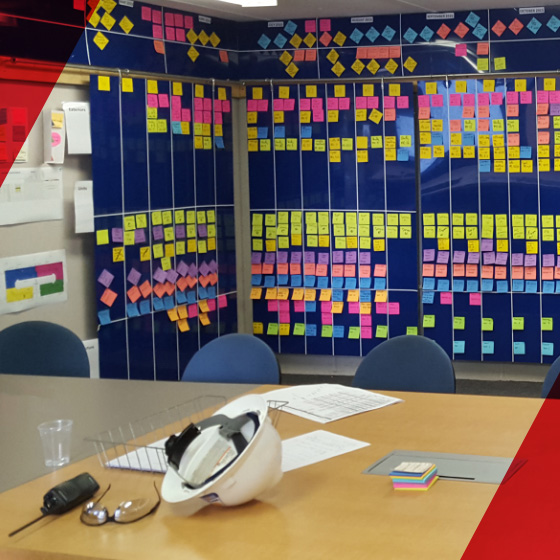
Preconstruction Schedule
The preconstruction schedule includes all design phase milestones as well as preliminary construction schedules. Using advanced scheduling software, we create a timeline that encompasses every aspect of the project’s construction. We begin with preconstruction, then as the construction activities are planned out and defined, our scheduling process includes:
- Planning: design, estimating, and key decision and reporting milestones.
- The Bidding Process: pre-qualification, bid release, pre-bid meetings, bidding and scope review, and subcontracting and procurement milestones.
- Plan Approval: regulatory requirements, permitting.
- Submittals and Mobilization: construction activities, material deliveries, and break-out schedules for major building components, sequences, or sub-activities as needed.
- Coordination of Owner-furnished Materials: “by-owner” systems, data/comm wiring and systems.
- Inspections: commissioning and testing, owner training.
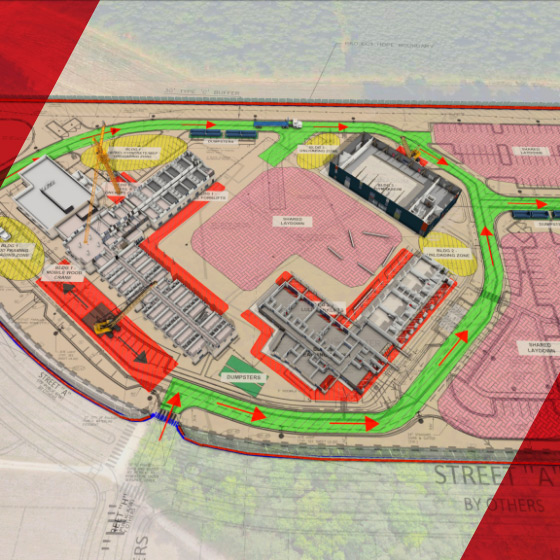
Logistics
The key to a successful construction project is communication which always starts with a well thought-out logistics plan. One of the first things we do is evaluate traffic flows and activity around the site. We want to assure the safety of everyone near the construction site and minimize any disruptions in the area. The Clancy & Theys construction team will develop a preliminary site logistics plan and work with all stakeholders to refine that plan for the needs of the community and surrounding areas.